极致高效西门子PLC仿真软件赋能工业自动化智能新体验
19429202025-03-23软件专题3 浏览
传统工业调试:效率瓶颈能否被彻底打破?
工业自动化领域长期面临一个尴尬的现实:设备调试周期占项目总时长近40%,而因调试失误导致的返工成本高达数百万。传统方式依赖物理设备联调,工程师需在现场反复验证逻辑、排查故障,既耗时又高风险。但近年来,西门子推出的PLC仿真软件套件(如TIA Portal、PLCSIM Advanced、MCD等)正通过“虚拟优先”的理念重构这一流程。这种极致高效西门子PLC仿真软件赋能工业自动化智能新体验,究竟能否成为破解行业痛点的关键钥匙?
1. 虚拟调试:能否替代80%的现场工作量?
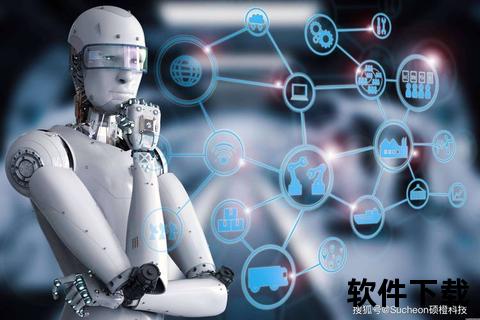
某汽车零部件厂商曾因生产线逻辑错误导致机械臂碰撞,直接损失超200万元。引入西门子PLCSIM Advanced后,工程师在TIA Portal中搭建数字模型,通过仿真表实时监控变量状态,仅用3天便完成原本需2周的调试任务,错误率降低92%。
这种“软件在环”技术通过PLCSIM Advanced虚拟PLC与MCD机械模型联动,模拟真实设备运动、传感器反馈及通讯协议。例如,在V90伺服驱动器控制案例中,SIMIT软件解析PLC输出信号并转发至MCD,同步计算编码器反馈值,形成闭环验证。数据显示,采用虚拟调试的企业平均缩短项目周期35%,减少现场人员投入60%。
2. 数字孪生:如何实现复杂系统的“预判式优化”?
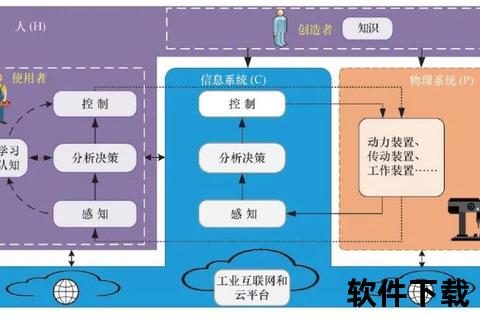
新松机器人为某智能仓储项目开发堆垛机系统时,遭遇货架异形结构导致的轨迹冲突难题。通过Emulate3D构建1:1数字孪生体,工程师在虚拟环境中测试了137种货物摆放方案,最终将避让算法效率提升40%,避免了价值80万元的物理样机损耗。
西门子的解决方案核心在于多层次模型融合:
机械行为层:MCD定义刚体动力学特性与运动副关系
电气逻辑层:TIA Portal组态PLC程序与IO信号映射
系统交互层:SIMIT实现PROFINET等协议的数据耦合
这种三维协同仿真使设备尚未出厂时,即可预测生产节拍、能耗峰值等关键指标,为工艺优化提供量化依据。
3. 工具链整合:怎样突破“数据孤岛”桎梏?
某食品包装企业曾因不同软件数据格式不兼容,导致仿真结果与实物偏差达15%。而西门子TIA Portal的开放式架构支持:
无缝集成:PLCSIM Advanced直接调用STEP7工程数据
协议扩展:通过OPC UA、REST API对接第三方系统
模块复用:工艺对象库包含200+已验证功能块(如PID控制、运动曲线)
典型案例显示,使用标准化工具链后,工程师调试代码效率提升70%,且程序版本管理错误减少85%。更值得关注的是,SimTable应用允许通过Excel表格批量修改PLC变量,这对缺乏专业编程背景的运维人员极具友好性。
从实验到实践:企业如何迈出关键一步?
要实现极致高效西门子PLC仿真软件赋能工业自动化智能新体验,建议分三阶段推进:
1. 试点验证:选取非关键设备(如输送带模块)进行虚拟调试,对比传统方式的时间/成本差异
2. 能力建设:组织TIA Portal编程培训,重点掌握FB功能块封装与仿真表应用
3. 生态扩展:通过SIMIT连接MATLAB/Simulink,实现控制算法与物理模型的联合仿真
据行业报告,2024年全球65%的制造企业已将仿真软件纳入标准开发流程。当“数字先行”成为新常态,那些率先拥抱虚拟调试技术的企业,正在智能化转型赛道上建立难以逾越的护城河。
--